Algorithms and Inventory
Inventory tracking algorithms, sorting algorithms, and shipping algorithms are the most common algorithms used to track, order, and ship inventory from a distribution center. Inventory tracking algorithms monitor and manage product stock levels in the distribution center. These algorithms also determine when new products must be ordered and when existing products must be reordered. First in, first out (FIFO) and Last in, First Out (LIFO) are the two most common inventory tracking algorithms (LIFO). FIFO tracks inventory that is received and sold in chronological order, whereas LIFO tracks inventory that is received and sold in reverse chronological order. Average Cost, Specific Identification, and Periodic are some other common inventory tracking algorithms. Specific Identification tracks inventory based on specific attributes such as serial numbers, whereas Average Cost values inventory based on the average cost of items purchased. Periodic inventory is tracked at regular intervals, such as the beginning and end of the month.
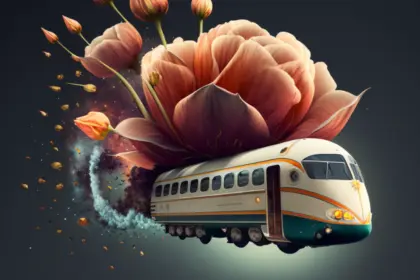
Sorting algorithms determine the most effective way to sort products in a distribution center. To determine the most efficient way to sort the products, these algorithms consider their size, weight, shape, and other characteristics. Quick Sort, Insertion Sort, Selection Sort, Merge Sort, and Bubble Sort are the most common sorting algorithms. Quick Sort is a fast algorithm for sorting large datasets. Insertion Sort is a straightforward algorithm for sorting items by comparing them one at a time. Selection Sort is a sorting algorithm that finds the smallest item in a list and moves it to the top. Merge Sort is a recursive sorting algorithm that divides the dataset into two halves and sorts each half separately. Finally, Bubble Sort is a sorting algorithm that compares adjacent items and swaps them if they are out of order.
The best way to package and ship products from the distribution center is determined by shipping algorithms. These algorithms take into account the product's size, weight, and shape, as well as the desired delivery times and locations. They also take into account any regulations or restrictions on shipping specific products. Route Optimization, Multi-Stop Routing, and Load Consolidation are the most common shipping algorithms. The shortest or most cost-effective routes for shipping products from one location to another are discovered by route optimization. Multi-Stop Routing determines the best order to ship products to multiple locations. Load Consolidation is the process of consolidating multiple orders for the same destination into a single shipment. Cost Backhauling, which identifies the most cost-effective return trips for a truck, and Load Balancing, which assigns the most cost-effective trucks and routes for a given shipment, are two other common shipping algorithms.
In addition to tracking, shipping, and sorting algorithms, fuzzy math can be used to sort and restack a pallet with different products by developing a fuzzy logic system. This system would identify the products on the pallet and determine the best way to sort and stack them using fuzzy logic and fuzzy sets. First, the system would need to recognize the various products on the pallet. This could be accomplished by collecting data about the products on the pallet using sensors, such as size, weight, shape, color, and texture. The information gathered would then be used to generate fuzzy sets for each product. The system would then need to figure out the best way to sort and stack the products. This could be accomplished by defining the relationships between the various products on the pallet using fuzzy rules. These rules could consider each product's size, weight, shape, color, and texture, as well as the desired stack height and space between products. Finally, the system must carry out the sorting and stacking process. This could be accomplished by using a robotic arm to move the products on the pallet in accordance with the previously defined fuzzy rules. The robotic arm would be able to move the products quickly and precisely, resulting in a more efficient and organized sorting and stacking process.